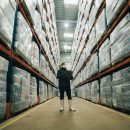
Spotless Supply Chains: Promoting Proper Hygiene in Warehouses
We don’t need to tell you that, in light of the ongoing pandemic, hygiene has become a more prominent issue than ever before across all customer-facing industries. In warehouses, this is particularly crucial due to the sheer volume of products that travel in and out of these environments on a daily basis.
With this in mind, today we’re showing you how to encourage spotless supply chains. Not only will this ensure the safety of your warehouse employees day to day, but it can also help make internal practices more efficient in the process – a real win-win!
Update your cleaning schedule
We’re sure you already have a regular cleaning routine for your warehouse, but following the outbreak of COVID-19, updating processes to be in line with new guidelines is of paramount importance. Focus on two elements: the extent of the clean and the time of the clean.
To optimise cleanliness, a quick wipe down at some point of the day simply won’t cut it anymore. Cleaning processes should be thorough, using disinfectant with over 70% alcohol to effectively kill germs lingering on surfaces.
Ideally, a deep clean should be scheduled every night after the departure of your warehouse employees. This will ensure areas aren’t quickly reinfected after cleaning, as well as help cleaning and warehouse staff adhere to social distancing guidelines.
Use labelling and taping effectively
On the topic of social distancing, clear labelling and taping has become a distinctive characteristic of warehouses up and down the country. With that in mind, look to promote hygiene in your warehouse by utilising these tools effectively – this can be done in two ways.
Firstly, use warning tapes on floors in areas of heavy foot traffic to reinforce the latest social distancing guidelines. Similar to new queuing systems in supermarkets, this will help your employees envision what 1 or 2 metres actually looks like, ensuring they keep safe distances from colleagues.
Secondly, look to improve your labelling systems for a more efficient stock identification process. Employees should be able to locate and source items at a glance to prevent any unnecessary contamination from sifting through mountains of stock. By creating a simple and logical labelling system, your warehouse can benefit from better sanitation and more efficient product picking.
Utilise PPE correctly
PPE or personal protective equipment, has been dominating national news recently – yet it’s not just the NHS frontline staff that require this as part of their daily operations.
PPE has been vital to warehouse workers for many years – however never has it been more important than right now. While PPE such as hard hats and hi-vis jackets remain an everyday essential, wearing gloves and masks should also be a priority for staff.
If your warehouse handles airborne substances and hazardous materials, it’s likely you may already have respiratory protection and gloves in stock. However, these should no longer be worn on an ‘as needed’ basis. Instead look to instill the importance of wearing PPE amidst the current pandemic in your workers at all times.
Consider your storage solutions
To make this process smoother still, you should also consider your storage solutions. Without the proper care and attention, storage areas can be breeding grounds for bacteria and germs, undermining your efforts to create a spotless working environment.
With the rest of your processes now optimised for cleanliness, consider how you can adapt your storage to best complement these changes. For example, opting for high-quality, practical shelving systems that can be easily cleaned and accommodate stock levels without overcrowding will help bolster the aforementioned labelling and cleaning systems.
Promoting a greater consciousness surrounding the cleanliness of your warehouse doesn’t require you to go back to the drawing board. With the correct know-how and some simple updates to current practices, you can take the right steps to protect the safety and sanitation of your warehouse and staff, with the added benefit of making day-to-day operations more efficient in the process!
Author bio:
Tom Brialey is the Founder and Director of Action Storage, which adopts his philosophy that, in addition to the highest quality products, you must also provide the highest standard of service to your customers in order to succeed. That’s why it’s Tom’s mission to provide expert support 100% of the way.